COMPANY INSIGHT
Come on – it’s just a plastic closure!
When discussing the development of a beverage closure with someone outside the industry, we often hear the saying: “Come on, it’s just a plastic closure! Developing such a simple piece of plastic cannot be that hard!”. Well, it is.
Written by Dr. Michael Krueger, CEO of Corvaglia Mould AG
What might look simple from the outside reveals tremendous work of development if you look at it more closely. But before going into details of the closure product requirements we shall take a look at three major steps in the life of a closure and what makes developing them so difficult in each section. Firstly, we talk about manufacturing of closures, secondly, we talk about the application of closures and thirdly, we talk about the usage by consumers.
Food trays and baking molds made from Genuine Vegetable parchment are biodegradable and home compostable.
Robust enough to tolerate variability
Obviously, a beverage closure is a mass product. Hundreds of billions of beverage closures only for PET containers are being used per year. This scale – together with standardization of neck finishes – gives our industry the chance to reach very high efficiency levels. The result is high cavity molds with short cycle times. The challenge is not to manufacture one hundred closures every two seconds on one line but to manufacture one hundred ‘good’ closures every two seconds. Requirements for a ‘good’ closure design start with robustness. If we only take a look at material diversity as an example: we have sampled more than a hundred different organoleptic HDPE resin grades with our closure designs over the last years. A ‘good’ closure design should manage to result in ‘good’ closures with the vast majority of these resin and masterbatch grades. A ‘good’ closure design also needs to be robust enough to balance variations of manufacturing equipment.
Precise enough to guarantee high speeds
If we follow the value stream of beverage closures, the next set of requirements stems from application of the closure on the bottling lines. Bottling lines handling more than 2’000 bottles per hour per capping head have become frequent sights. High speeds usually mean tolerances for processed parts become tighter. Especially as allowable reject rates – naturally – have not been increased along with the challenges. So even though everything around the closure design can change, closures need to be reproducible in vast quantities. In other words, the first cap must look and perform exactly like the last.
Performance at the limit
So far we have only talked about requirements stemming from manufacturing and application of the closure. Most closure functions aim at fulfilling requirements of the final product – the filled bottle. These requirements can be categorized as follows: safety requirements, tightness requirements, ergonomic requirements, environmental requirements and design requirements. corvaglia performs forty different laboratory tests to validate a closure or closure design against requirements of the final product. Passing forty different tests while being identical in vast numbers and robust enough to tolerate that everything around it can change. Not bad for a simple piece of plastic, is it?
Most of the requirements and challenges discussed are valid for the complete beverage package (i.e. bottle + closure) but it is important to state and understand that most of the functions of the package are defined by the closure and not the bottle.
The part of the bottle that interacts with the closure (the neck finish) is more or less standardized in certain categories. The closure needs to take care that all the functions at the interface between bottles and closures are guaranteed.
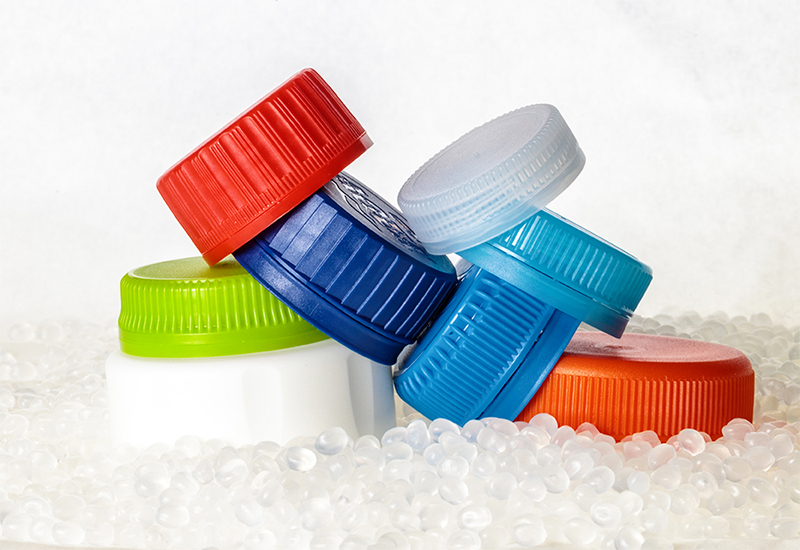
Facing the requirements
We have discussed a lot of different requirements. It is not exactly rocket science but in order to be successful you need expertise along the complete value creation chain and intelligent closure designers. You cannot empirically try out all combinations. You can also not run a computer simulation with those combinations to optimize the problem, because there is so many different laws and interactions that govern the problem. You need a team with experience, know-how and a good gut feeling to limit the number of simulations you run and the number of empirical trials you do.
The vast volume of beverage closures gives our industry the chance to be efficient. Every tiny material saving realized will have a gigantic effect on material and energy consumption along the value chain – and ultimately cost. Unfortunately, most of the requirements are harder to realize with
less material in the closure. So lightweighting is the ultimate challenge that makes closure development so tedious.
From good closure design to a good closure
When balancing requirements is so delicate, it is crucial to understand requirements in detail. So being close to the stakeholders that set the requirements is obviously essential. What definitely helps to get the right inputs is to have closure manufacturing in house with our manufacturing sites in Switzerland, Mexico and until the end of the year 2018 also in the United States.
In-house manufacturing not only helps to contribute to a good closure design. An efficient and highquality manufacturing operation is necessary to generate good closures from a good closure design.
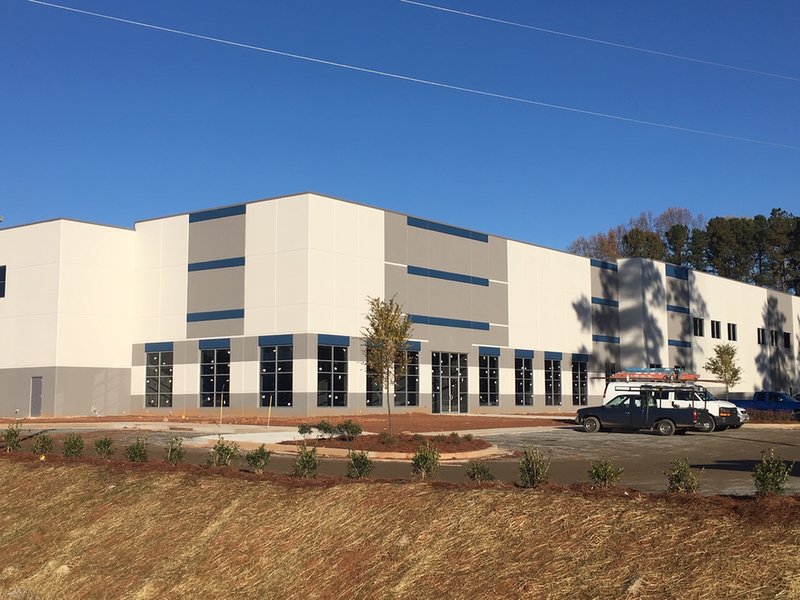
Image of Corvaglia closure manufacturing site in Newnan, GA, close to Atlanta
Contact Information
Corvaglia Mould AG
Hoernlistrasse 14,
Eschlikon
8360
Switzerland
Email: info@corvaglia.ch
Website: www.corvaglia.ch