Water and Wastewater Technology
Water Reuse
Reuse of Vapor Condensates
Resource and Energy Recovery
Zero Liquid Discharge
Cooling Water Management
Remote Maintenance
Meet us at Brau Beviale
Where: Nuremburg, Germany
Hall 6, Stand 245
Date: 13 – 15 November 2018
Discover new developments!
▲
▼
Saving resources: discover hidden potentials
Food manufacturers use water for many different stages in the production process. There are often potential savings to be made here in terms of resources and energy. For example the production of milk powder: Around 880 millilitres of water, the vapour condensate, is removed from a single litre of raw milk. Once treated into drinking water quality, the vapour condensate can then be used as cleaning water or for cooling processes so the dairy does not have to waste fresh water.
Read more
The EnviroChemie water specialists consider the entire chain as a whole. With the appropriate systems waste can be converted in resources or can supply energy. Whey, for example, can be converted into biogas in special anaerobic reactors, which in turn can be used to power other parts of the production process or the company as a whole. When other organic residues, e. g. product returns, and wastewater components are decomposed in special anaerobic reactors, the yield of biogas will increase significantly.
Read more
With BOT (Build Operate Transfer) concepts EnviroChemie offers a continuous improvement process. This is where the specialists take the reins at customers’ water treatment plants to implement process optimisations. It goes without saying that water and energy can both be saved, but this is also particularly appealing to many companies from a CSR perspective, or even for an energy audit.
Saving resources: discover hidden potentials
Food manufacturers use water for many different stages in the production process. There are often potential savings to be made here in terms of resources and energy. For example the production of milk powder: Around 880 millilitres of water, the vapour condensate, is removed from a single litre of raw milk. Once treated into drinking water quality, the vapour condensate can then be used as cleaning water or for cooling processes so the dairy does not have to waste fresh water.
The EnviroChemie water specialists consider the entire chain as a whole. With the appropriate systems waste can be converted in resources or can supply energy. Whey, for example, can be converted into biogas in special anaerobic reactors, which in turn can be used to power other parts of the production process or the company as a whole. When other organic residues, e. g. product returns, and wastewater components are decomposed in special anaerobic reactors, the yield of biogas will increase significantly.
With BOT (Build Operate Transfer) concepts EnviroChemie offers a continuous improvement process. This is where the specialists take the reins at customers’ water treatment plants to implement process optimisations. It goes without saying that water and energy can both be saved, but this is also particularly appealing to many companies from a CSR perspective, or even for an energy audit.
EnviModul modular process water and wastewater treatment plants
Using modular EnviModul plants, we can customize process water purification and wastewater treatment to meeting the required limit values.
The EnviModul machine housing includes all of the necessary mechanical and electrical equipment and is installed around pre-fabricated tanks at the customer site.
Thanks to the modular plant system we make it easy for you. We reduce the project complexity. We just need to connect it to your infrastruture. We put the EnviModul into service at your premises. Depending on the application we join three to twelve modules together.
Swipe gallery ⇔
Complex biological wastewater treatment plant expanded during normal operation
Fidel Dreher, a manufacturer of a range of juices, concentrates and purées, produces approximately 136,500 m³ of wastewater each year as a by-product of handling apples. The company wanted to expand its production capacity, which meant plans were to extend the existing wastewater treatment plant with biogas generation from the treated wastewater. The features include a Biomar anaerobic high-performance reactor, with a COD breakdown of approx. 90%, complete with innovative gas discharge system. The bioreactor generates up to 3600 m³ of biogas per day, which equates to an output of up to 1000 kW.
Read more
The entire facility came equipped with fieldbus technology and its own remote access system to two separate servers. When it came to building the plant, the fact that space was at such a premium posed a real challenge. The new plant was built and put into operation over three construction phases within in just seven months. During this period the plant controls were permanently adapted to suit the changing conditions.
“Time wasn’t on our side, so the warm start-up took place directly with original wastewater during normal operation. The process proved successful and was completed on schedule.” explained a Fidel Dreher employee.
▲
▼
Complex biological wastewater treatment plant expanded during normal operation
Fidel Dreher, a manufacturer of a range of juices, concentrates and purées, produces approximately 136,500 m³ of wastewater each year as a by-product of handling apples. The company wanted to expand its production capacity, which meant plans were to extend the existing wastewater treatment plant with biogas generation from the treated wastewater. The features include a Biomar anaerobic high-performance reactor, with a COD breakdown of approx. 90%, complete with innovative gas discharge system. The bioreactor generates up to 3600 m³ of biogas per day, which equates to an output of up to 1000 kW.
The entire facility came equipped with fieldbus technology and its own remote access system to two separate servers. When it came to building the plant, the fact that space was at such a premium posed a real challenge. The new plant was built and put into operation over three construction phases within in just seven months. During this period the plant controls were permanently adapted to suit the changing conditions.
“Time wasn’t on our side, so the warm start-up took place directly with original wastewater during normal operation. The process proved successful and was completed on schedule.” explained a Fidel Dreher employee.
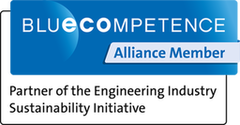